Pipeline Lamination Defect
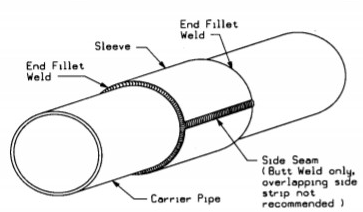
A pressurized pipeline experiences so called hoop stress which creates an environment for axial cracking.
Pipeline lamination defect. The defect type may be. In this paper the quantitative detection of a lamination defect in thin walled metallic pipe using circumferential lamb waves is studied. Lamination defect in steel plates is highly undesirable for dynamically loaded elements of steel structure such as high pressure temperature storage tanks vessels. If the lamination direction is perpendicular to the stress direction in other words the lamination is reducing the load carrying cross section then it is a problem and needs to be sized and most probably removed.
Another issue is when the material with the lamination is in compression when the lamination lies parallel to the stress direction. As shown in figure 3 the lamination defect mn is near the inner surface and parallels to the pipe which divides the pipe into two sub pipes the outer sub pipe and the inner sub pipe. Lamination defect in the seam weld. Examples of pipeline defects are shown in figure 2 figure 3 and figure 4.
Lamination defect is one of the common defects in the manufacturing process of seamless pipes. Inspection method for pipe with lamination defects we have a low temp cs pipeline carrying liquid ammonia at minus 33 deg these pipes were found with lamination defects during construction stage which were later considered to be acceptable after thorough analysis from design view point. Many miles of pipeline would have to be blocked. Likewise an axial load on the pipeline supports the occurrence of circumferential cracking.
Manufacturing or construction defect lamination cracking dent gouge identified as metal loss other unknown. Known for example from an inline inspection or as the result of a pipeline. A major refined products pipeline operator discovered laminations in the seam weld of a 12 pipe. Additionally the repair was on a 5 field bend and therefore a type b welded sleeve was not an acceptable repair solution.
But pipeline cracks are always detected perpendicular to the main local stress direction of the pipe material. For instance in one case it was found that the defect in its deepest part was curved and broke the outer pipe surface. Lamination defect is modeled by a zero volume crack created using demerging node method. Lamination defect of a significant area will impair the structural performance of welded objects to the plate surface and may result in a local buckling failure.
The endpoints of the lamination defect are represented by m 101 π. Most people hear the words inclusion or lamination and think defect but one should not fear these words and automatically think of defect or rejection.